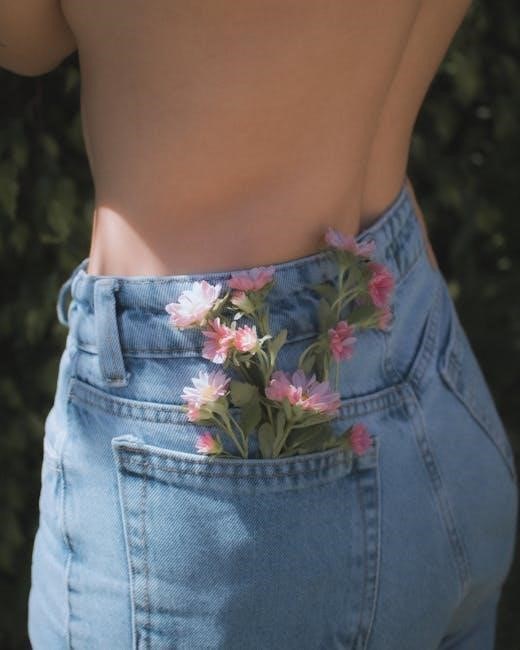
pocket hole screw length guide
Pocket hole screws are essential for creating strong, hidden joints in woodworking. Their length, type, and thread are crucial for ensuring stability and durability in various projects.
What Are Pocket Hole Screws?
Pocket hole screws are specialized fasteners designed for creating strong, hidden joints in woodworking projects. They feature a self-tapping tip and a unique thread design that allows them to securely anchor into wood without splitting it. These screws are typically used in conjunction with a pocket hole jig, which drills angled holes for the screws to fit into. They come in various lengths and thread types, making them suitable for different materials and project requirements. Correct screw selection is vital to ensure proper joint strength and durability, as outlined in a detailed pocket hole screw length guide.
Importance of Using the Correct Screw Length
Importance of Using the Correct Screw Length
Using the correct screw length is critical for ensuring strong, durable joints in woodworking projects. A screw that is too short may not provide adequate holding power, leading to weak joints, while a screw that is too long can split the material or protrude from the other side. Proper screw length ensures the threads fully engage with the wood, creating a secure connection. This is especially important for maintaining structural integrity in furniture, cabinets, and other projects. Referencing a detailed pocket hole screw length guide helps in selecting the optimal screw for specific materials and joint types, avoiding common mistakes.
Understanding Pocket Hole Screw Components
Pocket hole screws consist of a head, threads, and shaft. The head type and thread design ensure proper driving and material engagement. Coatings enhance durability and prevent rust.
Screw Head Types and Their Uses
Pocket hole screws feature various head types, each designed for specific applications. The pan-head is the most common, offering a broad seating area for secure fastening. Flat-head screws are ideal for flush surfaces, while round-head or button-head screws provide a decorative finish. The head type determines how the screw sits in the material, ensuring proper seating and strength. Coatings like zinc or stainless steel enhance durability. Choosing the right head type ensures optimal performance and appearance in woodworking projects, while improper selection can lead to weak joints or unsightly protrusions.
Thread Types: Coarse vs. Fine
Pocket hole screws come with two primary thread types: coarse and fine. Coarse threads are larger and deeper, providing a stronger grip in softer materials like pine or plywood, while fine threads are tighter and more refined, suitable for hardwoods or thinner materials to prevent splitting. Coarse threads are ideal for general woodworking projects, offering excellent holding power, whereas fine threads are better for dense woods or when a more discreet joint is desired. Matching the thread type to your material ensures optimal strength and durability, making it a critical factor in achieving professional-grade results in your projects.
Choosing the Correct Screw Length
Correct screw length ensures joints are secure without causing wood splitting, providing optimal strength and stability in various woodworking applications.
Factors Affecting Screw Length
The correct screw length depends on material thickness, joint type, and wood species. Thicker materials require longer screws to ensure proper engagement without splitting the wood. Joint stress also impacts length, with heavier loads needing longer screws for added stability. Wood density plays a role, as hardwoods may require slightly shorter screws than softwoods to avoid over-penetration. Additionally, the angle of the pocket hole drill (typically 15 degrees) influences screw seating. Ensuring the screw is long enough to engage both pieces securely but not so long that it exits the back is critical for strength and a professional finish.
Material Thickness and Screw Size
Material thickness directly impacts the required screw size to ensure proper joint strength. For example, 1/2″ thick materials typically use 1″ screws, while 3/4″ thick materials require 1-1/4″ to 1-1/2″ screws. Thicker materials, such as 1-1/2″ stock, may need 2″ or longer screws for optimal engagement. The screw length must also account for the 15-degree angle of the pocket hole to prevent over-drilling or under-engagement. Using screws that are too short can result in weak joints, while screws that are too long may protrude from the back. Always consult a pocket hole screw guide for specific recommendations based on your material thickness and project needs.
Joint Type and Screw Length Requirements
The type of joint significantly influences the required screw length. For butt joints, screws should be long enough to securely connect both pieces without over-drilling. Lap joints often require slightly longer screws to ensure proper engagement through both layers. Miter joints may need shorter screws to avoid splitting the wood. Generally, screws should extend at least halfway into the second piece of material. Using screws that are too short can compromise joint strength, while overly long screws may protrude or cause splitting. Always consider the joint type and material thickness together to select the optimal screw length for a durable connection.
Screw Types and Coatings for Different Projects
Coated screws resist corrosion, ideal for outdoor use, while uncoated screws are better for indoor projects. Choose screw type based on project demands and material compatibility.
When to Use Coated vs. Uncoated Screws
Coated screws are ideal for outdoor or moisture-exposed projects, offering rust resistance. Uncoated screws are better for indoor use, where corrosion isn’t a concern. Choose based on project environment and material needs for optimal performance and cost-effectiveness.
Applications and Best Practices
Pocket hole screws are widely used in furniture making, cabinetry, and shelving for their strength and invisibility. For best results, ensure screws are appropriately sized for material thickness to avoid splitting wood. Always drill pilot holes to guide screws accurately and prevent misalignment. Use clamps to hold pieces steady during assembly for precise joints. Consider project requirements, like outdoor exposure, to choose coated screws for durability. Regularly maintain tools, such as jigs and drill bits, to ensure consistent performance. Proper spacing of screws, typically 2 inches from edges, enhances joint stability and prevents weakening of the material.
Common Mistakes to Avoid
- Using screws that are too short can result in weak joints, while screws that are too long may protrude or split the material.
- Over-tightening screws can cause the wood to crack or the joint to become unstable.
- Drilling pilot holes without proper alignment can lead to misaligned screws and uneven joints.
- Ignoring material thickness when selecting screw length can compromise the joint’s strength and durability.
Avoiding these mistakes ensures stronger, more professional-looking results in woodworking projects.
Mastering pocket hole screws ensures strong, precise joints. For more guidance, visit Kreg Tool or download a printable guide for easy reference.
Final Tips for Selecting Pocket Hole Screws
For optimal results, always match screw length to material thickness and joint type. Use coarse threads for softwoods and fine threads for hardwoods. Ensure screws don’t protrude from the backside. Clamp properly to avoid gaps. Test on scrap wood first. Keep a printable guide handy for quick reference. Proper selection ensures strength and durability in your projects.
Printable Pocket Hole Screw Guide
Printable Pocket Hole Screw Guide
A printable pocket hole screw guide is an invaluable resource for woodworkers. It provides a quick reference chart for selecting the correct screw length, type, and thread based on material thickness and joint requirements. The guide typically includes charts for different materials, such as softwoods and hardwoods, and offers recommendations for edge joints, T-joints, and angle joints. By printing and laminating the guide, you can keep it in your workshop for easy access. This ensures consistent, professional results and reduces the risk of errors. Many guides are available online for free, making it easy to find one tailored to your needs.